Case Study: Warehouse Optimization Through WMS Integration
In the world of modern logistics, efficiency is everything. For warehouses struggling with delays, stock errors, and disorganized workflows, implementing the right system can be transformative.
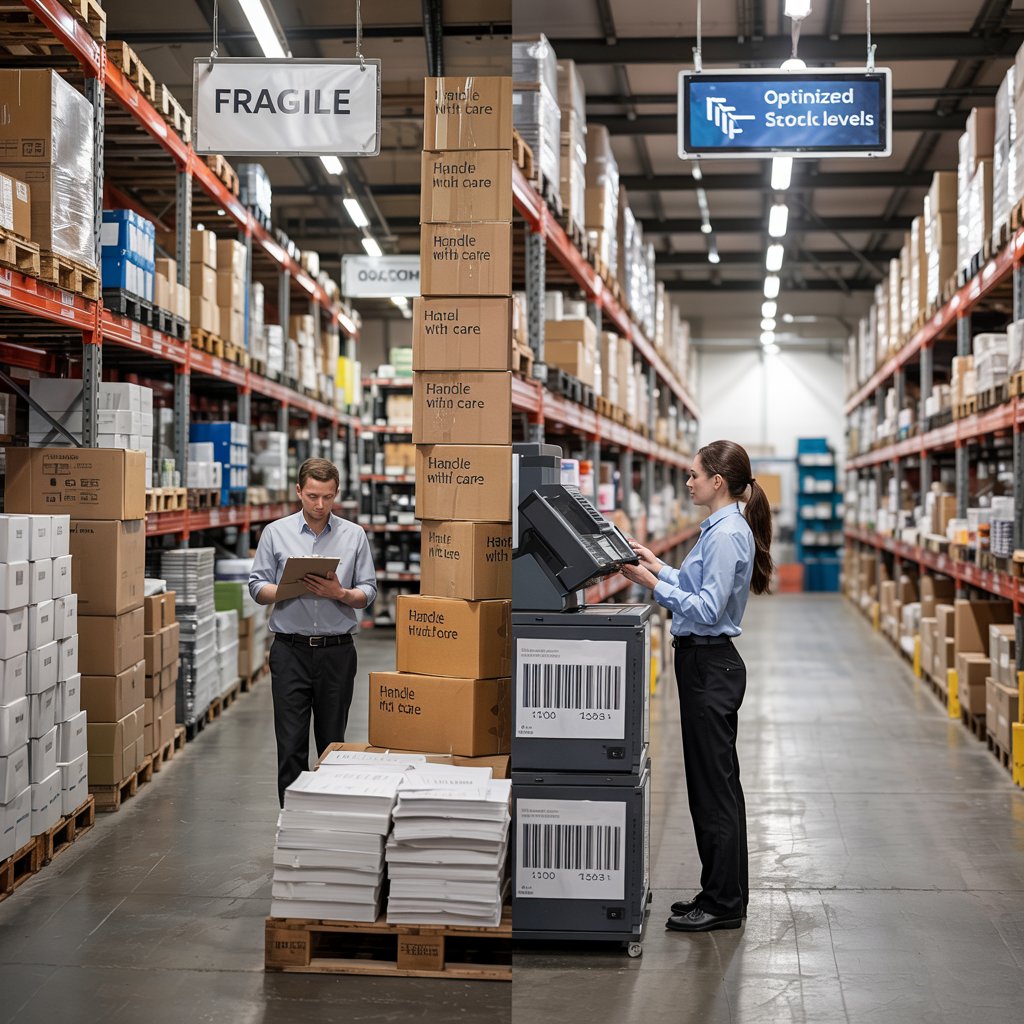
🏭 The Challenge: Manual Chaos and Inefficient Workflows
Company: A mid-sized 3PL provider with two warehouses in the U.S.
Inventory: Over 12,000 SKUs for 45+ clients
Team Size: 30 warehouse staff, 5 logistics coordinators
Pain Points:
- ❌ Inconsistent inventory counts
- ⏱️ Long order picking times
- 📄 Paper-based processes with frequent human errors
- 😩 Frustrated clients due to delays and lost products
Despite having a reliable team, the company struggled to scale and compete due to the manual nature of their operations.
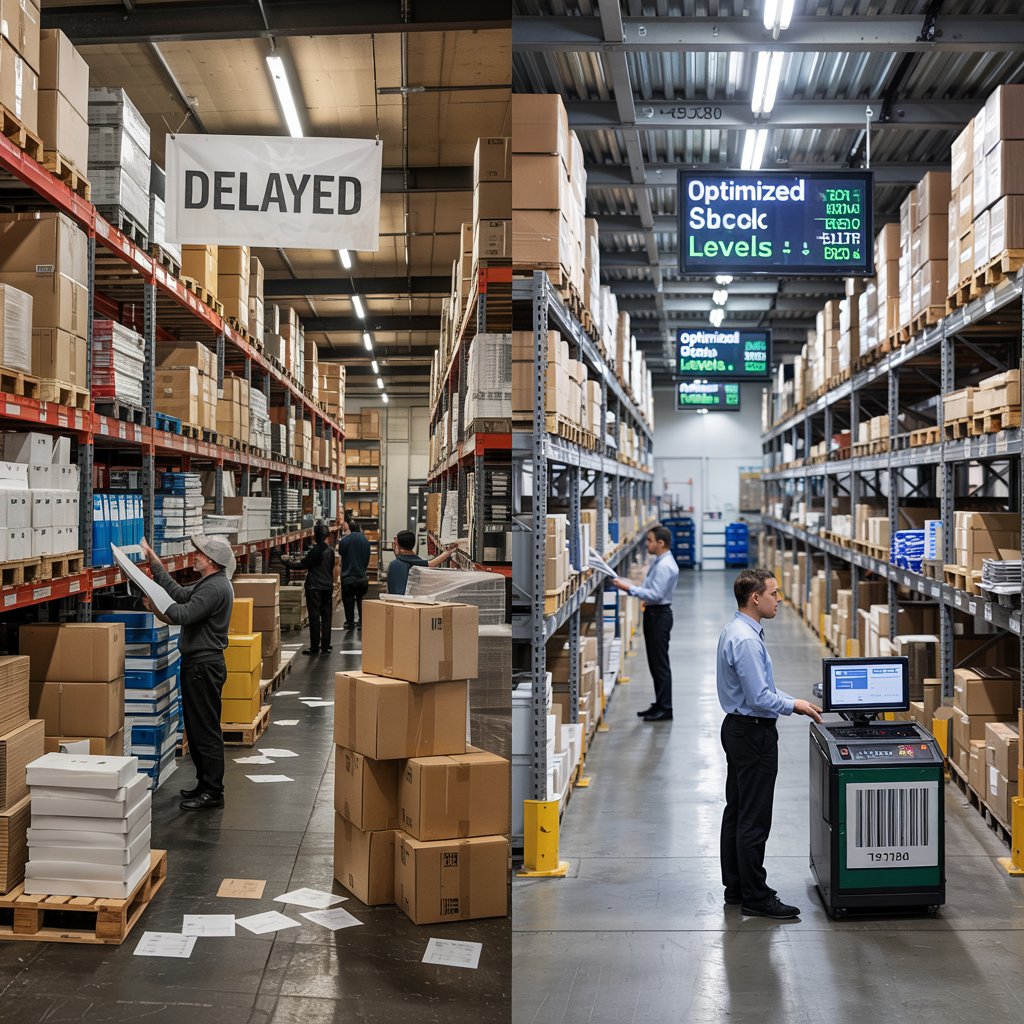
💡 The Solution: WMS Integration
After reviewing several software options, the company chose to implement a cloud-based Warehouse Management System that offered:
- Real-time inventory tracking
- Barcode scanning integration
- Customer access portal
- Task management and user role configuration
- Seamless inbound/outbound order processing
The chosen WMS allowed them to go fully digital within 30 days—without needing major IT infrastructure.
🔧 Implementation Strategy
Phase 1: Data & Process Mapping
- Digitized all SKU data
- Created zones and bin locations in the WMS
- Standardized receiving and picking workflows
Phase 2: Hardware Setup
- Deployed barcode scanners and label printers
- Connected WMS with existing ERP and shipping tools
Phase 3: Team Training
- Conducted role-based sessions for warehouse staff
- Created SOPs for scanning, packing, and order fulfillment
- Offered refresher training post-launch
📈 The Results: Real Improvements in 60 Days
Within just two months, the company saw measurable gains:
Metric | Before WMS | After WMS |
Inventory Accuracy | 86% | 99.2% |
Order Picking Time | 12 min/order | 6 min/order |
Client Complaints | Weekly | Near zero |
Order Throughput | +0% | +35% |
The WMS also provided real-time dashboards, allowing supervisors to identify bottlenecks and reassign tasks instantly—keeping productivity high.
🙌 Team Impact & Client Satisfaction
The Warehouse optimization case study team reported higher confidence and less stress:
“Before, we’d spend 15 minutes trying to find a SKU. Now, I scan it and know exactly where it is.”
— Carlos, Warehouse Operator
Clients also noticed the difference, praising the faster turnaround and order visibility through the customer portal.
🧭 Key Takeaways Warehouse optimization case study
- A cloud-based WMS can deliver fast ROI, even for mid-sized teams
- Proper onboarding and training are essential for adoption
- Digital tracking and scanning reduce error and boost speed
- Real-time visibility empowers both staff and clients
🚀 Final Thoughts Warehouse optimization case study
Warehouse optimization case study doesn’t require huge budgets or long delays. With the right WMS and a structured rollout, even small to medium operations can become more agile, efficient, and client-friendly.
Thinking of optimizing your warehouse? Learn from this case: digitize smart, train your team, and measure results early.