WMS Implementation Guide: From Setup to Success
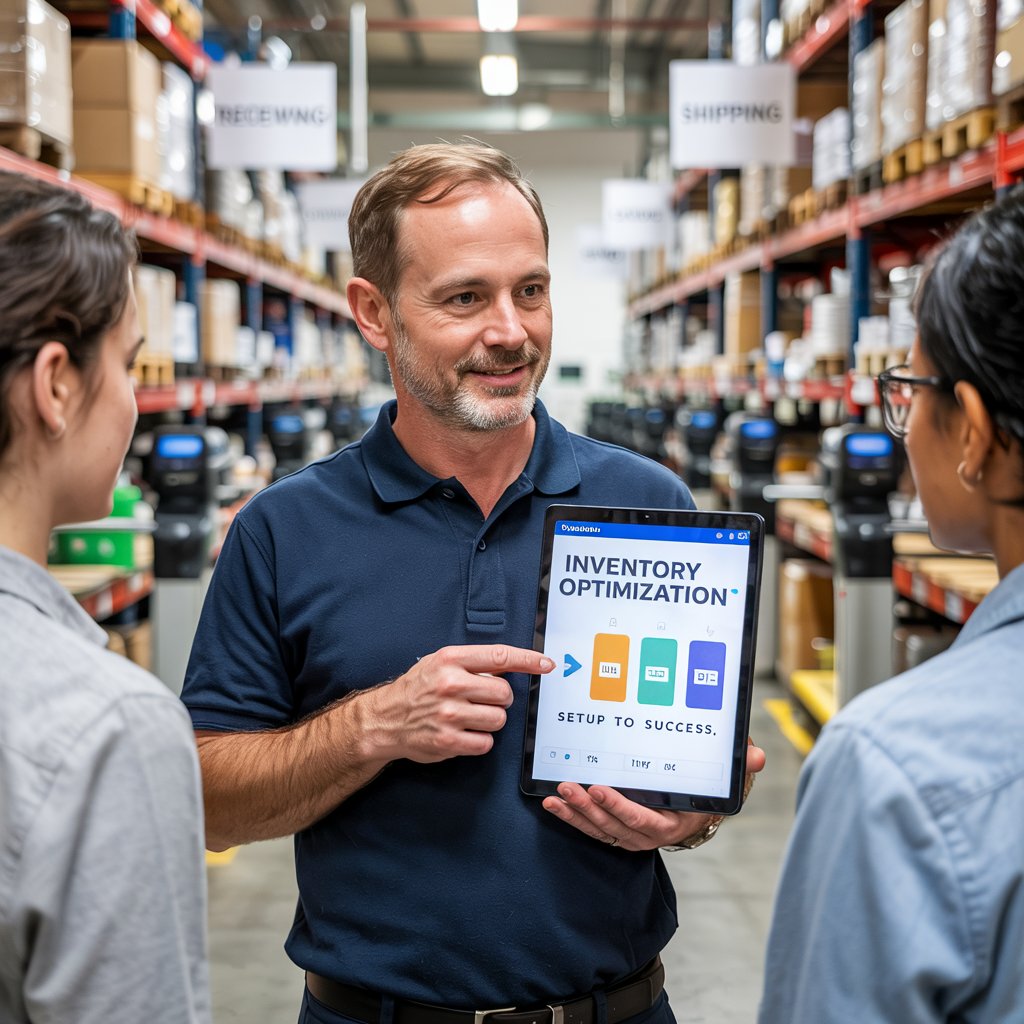
🔍 Step 1: Know What You Want to Fix
Start with a simple question:
Why are you implementing a Warehouse management software implementation in the first place?
Common answers:
- “We keep losing track of stock.”
- “Our team wastes too much time picking orders.”
- “Inventory numbers never match.”
Knowing your top pain points will help you choose the right features, prioritize rollout tasks, and measure success after launch.
🧠 Pro Tip: List your top 3 warehouse frustrations—and what “success” looks like if they’re solved.
🧩 Step 2: Get Your Warehouse in Order
Before touching the software, look at your physical warehouse:
- Are items clearly labeled and shelved?
- Do you have logical zones (receiving, packing, shipping)?
- Is there a standard way to do things—or does everyone “wing it”?
The more organized and consistent your current process is, the easier it will be to digitize it.
📦 Bonus Tip: Clean, label, and map your warehouse layout before configuration begins.
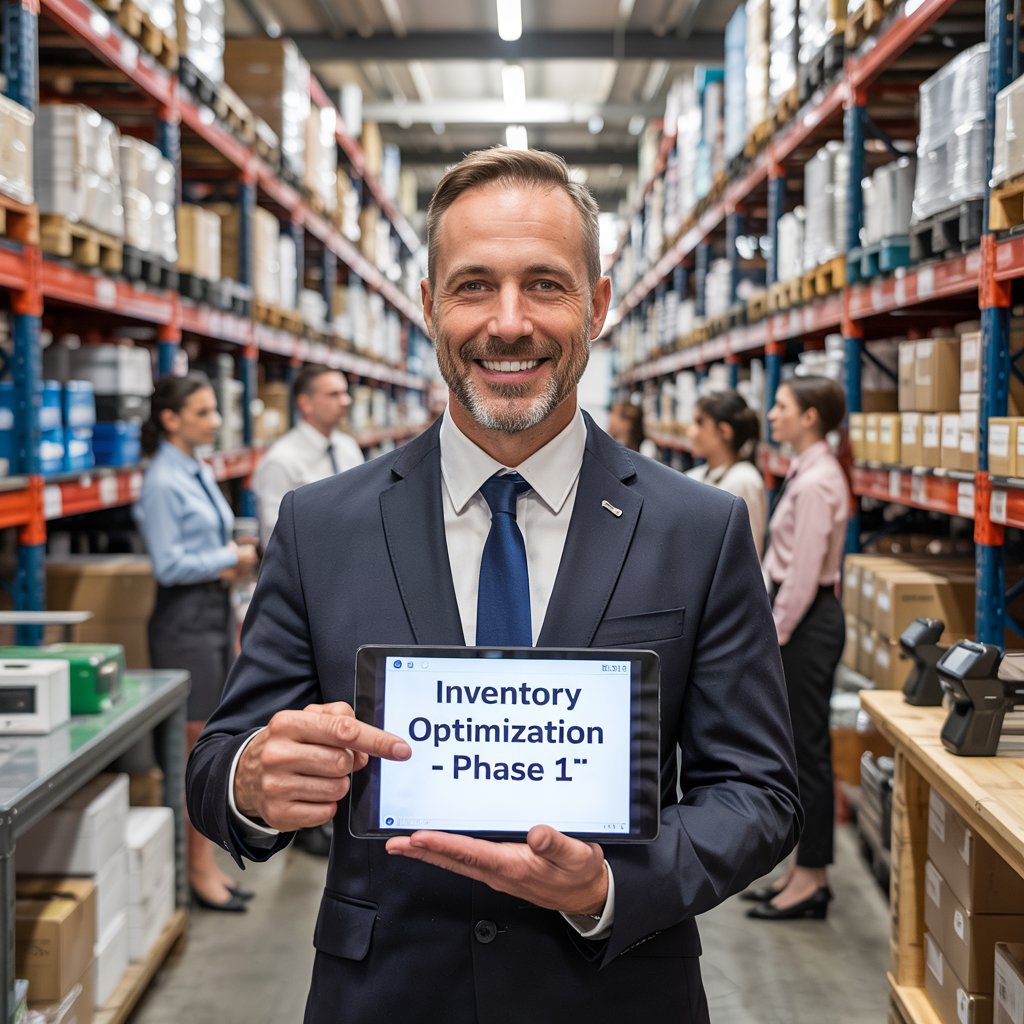
📊 Step 3: Prep Your Data
Time to get digital.
Make sure your item catalog, bin locations, SKUs, and stock levels are accurate and up to date. Incomplete or messy data is one of the biggest causes of delayed launches and post-implementation chaos.
🧹 Checklist:
- Remove duplicate SKUs
- Standardize units of measure
- Confirm item dimensions and weights
- Assign bin locations (even temporary ones)
⚙️ Step 4: Set Up Your WMS
Now the fun begins.
You’ll work with your WMS provider to configure the system to match your operations. This includes:
- Defining warehouse zones and bin logic
- Setting up users and access levels
- Integrating barcode scanners or label printers
- Importing your clean data
🏗️ Start simple. You can always expand to more complex workflows later.
🧪 Step 5: Test Everything
Before you go live, do a full run-through:
- Receive an item
- Put it away
- Pick and pack an order
- Ship it
- Count inventory
If something doesn’t feel intuitive or breaks down, now’s the time to adjust.
🎯 Goal: Make sure every workflow works—from the warehouse floor to the system backend.
👥 Step 6: Train Your Team (and Listen to Them)
Even the best WMS will fail if no one knows how to use it.
- Run hands-on training for staff by role
- Keep it simple—focus on daily tasks
- Create cheat sheets or quick-reference guides
- Ask for feedback during and after training
💬 Your team knows where the pain points are. Let them help shape better processes.
🚀 Step 7: Launch and Learn
Go live in phases if possible—start with one team, shift, or product area.
- Monitor key metrics (order accuracy, picking speed)
- Stay ready to fix bugs or tweak settings
- Celebrate small wins to build team momentum
📈 Most companies see big improvements in the first 30–60 days—if the rollout is managed well.
📌 Final Tips for a Smooth Warehouse management software implementation
- Appoint an internal champion to coordinate everything
- Keep communication open between teams
- Plan for downtime or delays—just in case
- Review progress weekly and keep iterating
🧭 Your Next Move
WMS implementation isn’t just a tech upgrade—it’s a Warehouse management software implementation . Done right, it brings clarity, speed, and control to every part of your operations.
So take it one step at a time, build your foundation carefully, and don’t forget: the goal isn’t just to “go digital,” but to make life easier for your warehouse and your business.