Tracking Warehouse KPIs: How Logistics Software Can Help
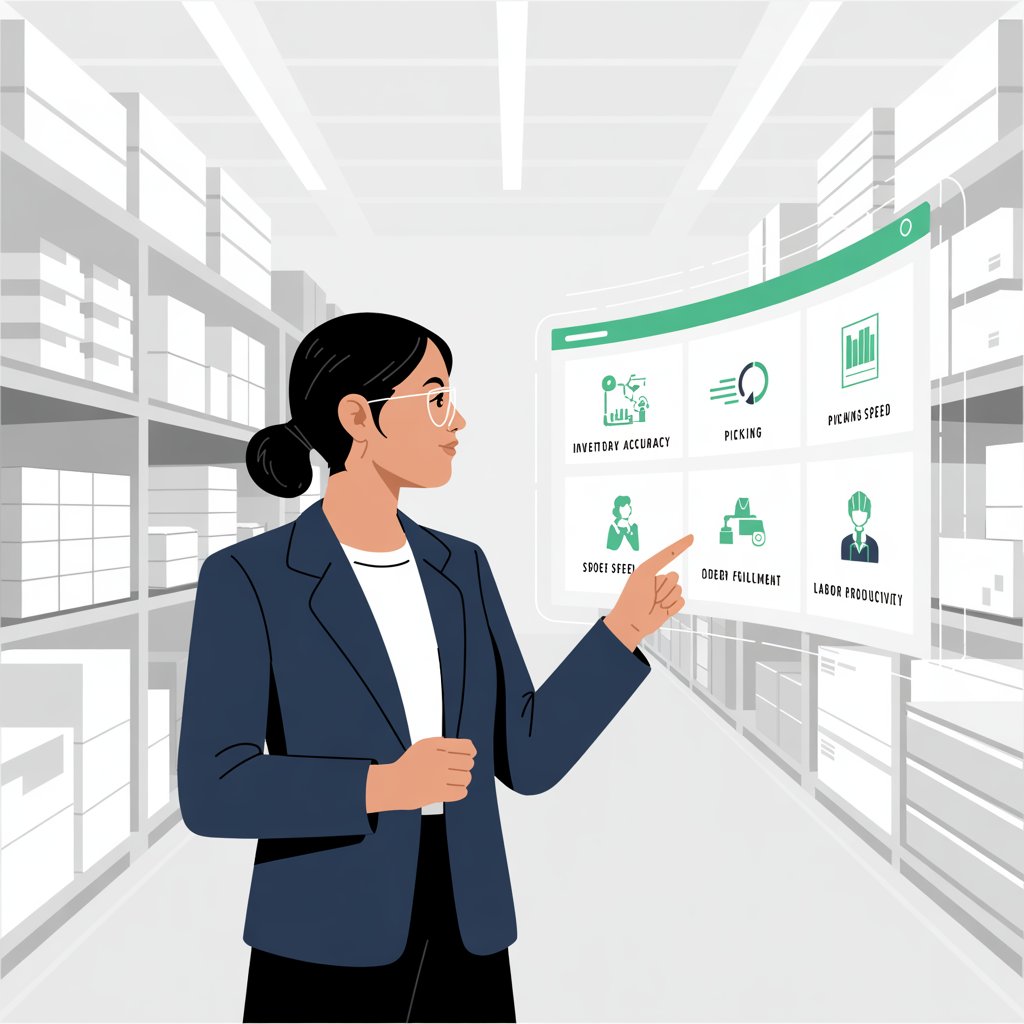
🔍 What Are Warehouse KPIs software and Why Do They Matter?
Warehouse KPIs are measurable metrics that provide visibility into performance areas such as inventory accuracy, order processing speed, labor efficiency, and more.
Monitoring them allows logistics teams to:
- Detect inefficiencies early
- Reduce costs and errors
- Improve customer satisfaction
- Benchmark performance over time
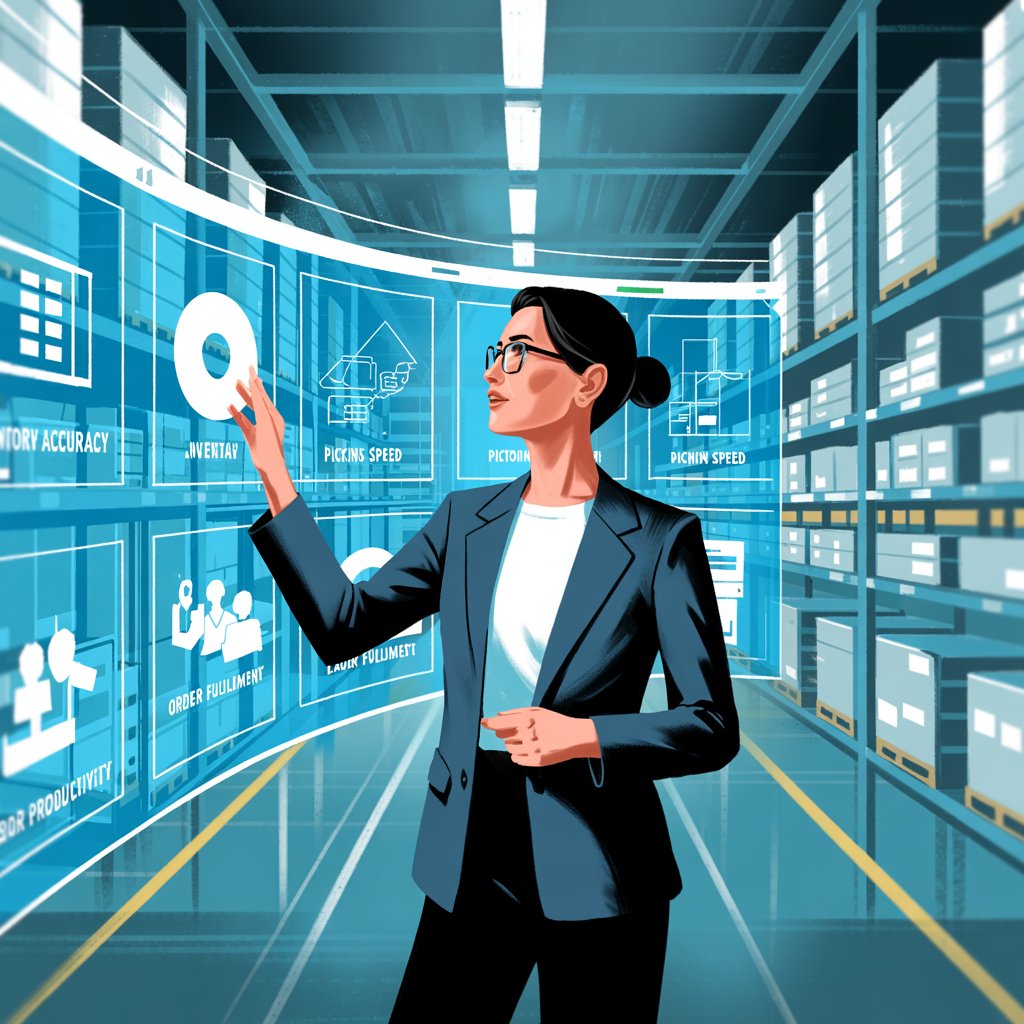
✅ 10 Essential KPIs Every Warehouse Should Track
Here are the most important warehouse KPIs — and what they reveal:
KPI | What It Measures | Why It Matters |
Inventory Accuracy | Stock vs. system data | Reduces over/understocking |
Order Cycle Time | Time from order to ship | Impacts customer satisfaction |
Picking Accuracy | Correct items per order | Minimizes returns and rework |
Carrying Cost of Inventory | Storage costs over time | Helps optimize stock levels |
Dock-to-Stock Time | Time to receive and store goods | Affects inbound efficiency |
Order Fill Rate | % of orders shipped completely | Indicates service level |
Labor Productivity | Orders/hour/employee | Tracks workforce performance |
Return Rate | % of returned orders | Flags quality or accuracy issues |
Warehouse Space Utilization | Space used vs. available | Informs layout efficiency |
Backorder Rate | % of orders delayed | Highlights inventory gaps |
📌 Tip: Choose KPIs that align with your warehouse type — 3PLs, ecommerce fulfillment centers, and manufacturing warehouses may prioritize different ones.
🧠 Challenges of Manual KPI Tracking
Many warehouses still rely on spreadsheets, paper logs, or disconnected systems to monitor performance. This leads to:
- Outdated or inaccurate data
- Lack of real-time insights
- Inability to spot trends quickly
- Higher risk of human error
🖥️ How Logistics Software Streamlines KPI Tracking
Modern WMS and logistics platforms are designed to automatically track and report KPIs, offering dashboards and alerts that drive smarter decisions.
Key benefits:
- Real-time data updates from every warehouse operation
- Custom dashboards that show top metrics at a glance
- Automated reports delivered daily, weekly, or monthly
- Drill-down capabilities to investigate root causes of issues
- Cross-system integration (TMS, ecommerce, ERP)
This not only improves visibility — it enables proactive action rather than reactive fixes.
🧩 Example: KPI Dashboard Features in Logistics Software
A robust WMS typically provides:
- Live inventory accuracy %
- Pick & pack times per order
- User productivity by shift
- Inbound vs. outbound volume
- Top reasons for returns or delays
With visual charts, trend lines, and color-coded alerts, warehouse managers can instantly identify what’s working — and what’s not.
📈 Final Thoughts
Tracking KPIs is no longer a nice-to-have — it’s a must for scalable, profitable logistics. With the right warehouse management software, teams can move from gut-based decisions to data-driven warehouse optimization.
Whether you’re managing one location or a multi-warehouse network, performance visibility is the first step to continuous improvement.