Blurry Barcode Solutions: Ensuring Accurate Inventory Scanning
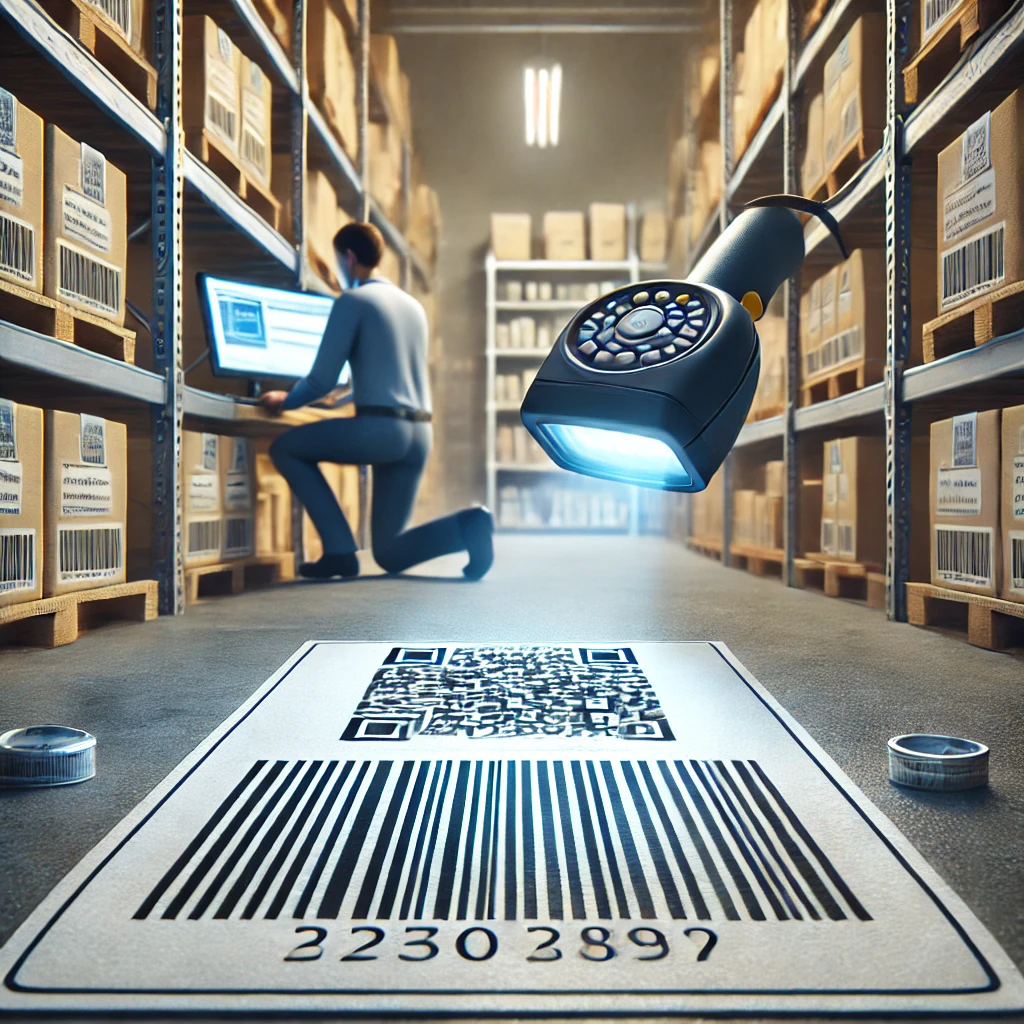
Understanding the Blurry Barcode Problem
Blurry barcodes can occur for various reasons:
- Poor printing quality
- Wear and tear on labels
- Incorrect scanner settings
- Environmental factors (humidity, temperature)
- Inadequate lighting conditions
The Impact of Blurry Barcodes
- Inaccurate inventory counts
- Slower checkout processes
- Increased manual data entry and human errors
- Customer dissatisfaction
- Revenue loss due to mispricing or misidentification
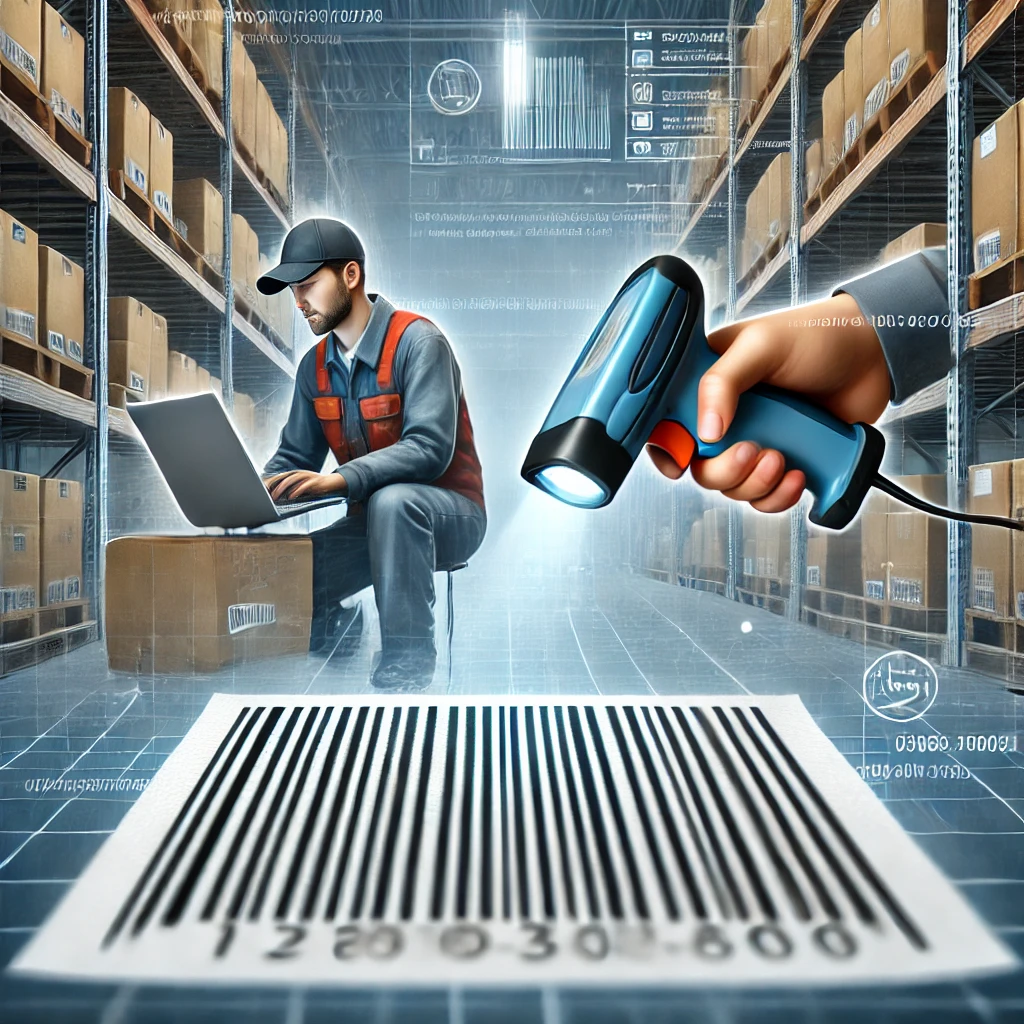
Solutions for Blurry Barcode Issues
1. Improve Printing Quality
- Use high-quality printers designed for barcode printing
- Ensure proper maintenance of printing equipment
- Choose appropriate label materials for your environment
Tip: Thermal transfer printers often produce more durable barcodes compared to inkjet printers.
2. Optimize blurry barcode Design
- Use appropriate barcode sizes for your products
- Ensure adequate quiet zones around the barcode
- Choose barcode symbologies that suit your needs (e.g., Code 128, QR codes)
3. Enhance Scanning Technology
- Invest in high-quality barcode scanners with advanced imaging technology
- Regularly update scanner firmware
- Train staff on proper scanning techniques
4. Implement Redundancy Measures
- Use duplicate barcodes on different sides of the product
- Implement a system for manual entry of product codes as a backup
5. Maintain Proper Lighting
- Ensure adequate, consistent lighting in scanning areas
- Consider using scanners with built-in illumination for challenging environments
6. Regular Maintenance and Cleaning
- Clean scanner windows regularly
- Inspect and replace damaged barcode labels promptly
7. Use Protective Coatings
- Apply laminate or UV-resistant coatings to barcode labels for added durability
8. Implement Quality Control Processes
- Regularly test barcode readability
- Establish a protocol for addressing problematic barcodes
Advanced Solutions for Persistent Issues
1. Image Processing Software
- Utilize software that can enhance and clean up barcode images before processing
2. Machine Learning Algorithms
- Implement AI-powered systems that can read even severely damaged barcodes
3. RFID Technology
- For environments where barcode scanning is consistently problematic, consider RFID as an alternative
Best Practices for blurry barcode Management
- Standardization: Use consistent barcode formats across your inventory
- Regular Audits: Conduct periodic checks of your barcode system’s effectiveness
- Staff Training: Ensure all employees understand proper scanning techniques and troubleshooting procedures
- Vendor Compliance: Work with suppliers to ensure incoming products have high-quality, readable barcodes
- Environmental Control: Manage temperature and humidity in storage areas to prevent label degradation
When to Seek Professional Help
If blurry barcode issues persist despite implementing these solutions, it may be time to consult with inventory management specialists or barcode system experts. They can provide tailored solutions for your specific business needs and environment.
The Future of Barcode Technology
As technology advances, new solutions are emerging to address barcode readability issues:
- Digital Watermarking: Invisible codes embedded in product packaging
- NFC Tags: Near Field Communication for close-proximity scanning
- Computer Vision: Advanced image recognition for identifying products without traditional barcodes
Staying informed about these developments can help you future-proof your inventory management system.
Conclusion
Dealing with blurry barcodes is an ongoing challenge in inventory management, but with the right strategies and tools, it’s a challenge that can be effectively managed. By implementing the solutions outlined in this guide, you can significantly improve the accuracy and efficiency of your inventory scanning processes.
While addressing blurry barcode issues is crucial, it’s just one aspect of efficient inventory management. Modern businesses require comprehensive solutions that integrate seamlessly with their existing systems. This is where specialized software solutions come into play.
Linbis, a leader in logistics software development, offers cutting-edge inventory management systems that can complement and enhance your barcode scanning processes. From custom development tailored to your unique needs to out-of-the-box solutions for immediate implementation, Linbis provides tools that can help businesses overcome challenges like blurry barcodes while optimizing their entire inventory management workflow.
By leveraging advanced technologies and industry expertise, Linbis helps businesses streamline their operations, reduce errors, and improve overall efficiency in inventory tracking and management. Whether you’re dealing with persistent barcode issues or looking to upgrade your entire inventory system, considering a specialized software solution can be a game-changer for your business operations.