Implementing a Barcode System: A Step-by-Step Guide for Small Businesses
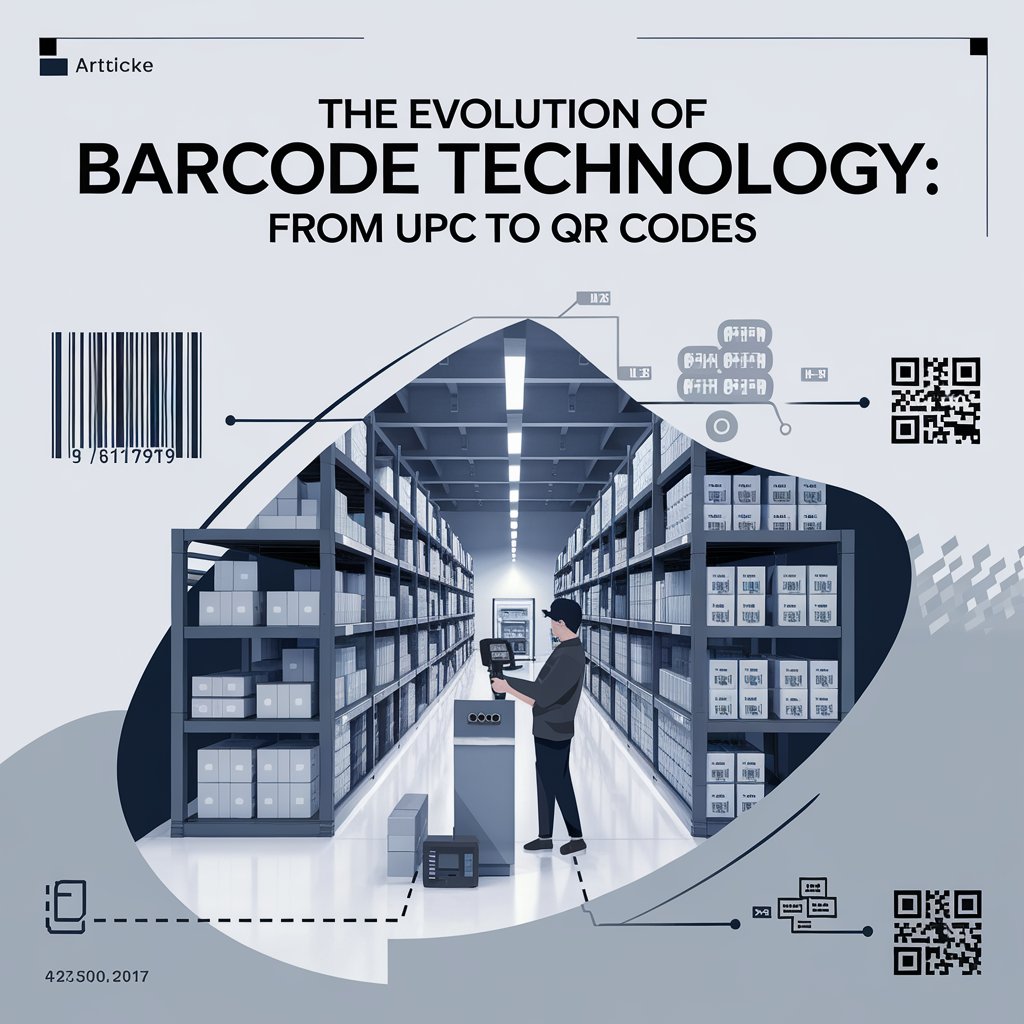
Why Implement a Barcode System?
Before diving into the implementation process, let’s quickly review the benefits of using a barcode system:
- Improved Accuracy: Minimize human errors in data entry and inventory counts.
- Time Savings: Quickly scan items instead of manually inputting data.
- Better Inventory Management: Real-time tracking of stock levels.
- Enhanced Customer Service: Faster checkout processes and improved product information access.
- Data-Driven Decision Making: Gather detailed data on sales and inventory movements.
Step-by-Step Implementation Guide
Step 1: Assess Your Needs
Begin by evaluating your business requirements:
- What items do you need to track?
- How many locations do you have?
- What information do you need to encode in the barcodes?
- What’s your budget for this project?
Step 2: Choose the Right Barcode Type
Select a barcode symbology that suits your needs:
- 1D Barcodes (e.g., UPC, Code 39): Good for simple product identification.
- 2D Barcodes (e.g., QR codes, Data Matrix): Can store more information, suitable for detailed tracking.
Consider industry standards and the amount of data you need to encode when making your choice.
Step 3: Select Barcode Software
Choose software that will generate barcodes and manage your inventory:
- Look for user-friendly interfaces.
- Ensure compatibility with your existing systems.
- Consider cloud-based solutions for easier access and updates.
- Check for reporting and analytics features.
Step 4: Invest in Hardware
Purchase the necessary equipment:
- Barcode Printers: Choose between thermal, thermal transfer, or laser printers based on your needs and budget.
- Barcode Scanners: Options include handheld, wireless, or smartphone-based scanners.
- Mobile Devices: If you’re using a mobile inventory management system.
Step 5: Set Up Your Inventory Database
Organize your product information:
- Create a comprehensive list of all your products.
- Assign unique identifiers to each item.
- Include relevant details like price, description, and supplier information.
Step 6: Generate and Print Barcodes
Use your chosen software to create barcodes:
- Generate a unique barcode for each product or SKU.
- Print barcodes on labels or directly on packaging.
- Ensure the barcodes are of good quality and easily scannable.
Step 7: Label Your Products
Apply the barcodes to your inventory:
- Ensure consistent placement for easy scanning.
- Use durable labels that can withstand handling and environmental factors.
Step 8: Train Your Staff
Educate your team on the new system:
- Provide hands-on training with the scanning equipment.
- Explain the importance of accurate scanning and data entry.
- Create standard operating procedures for barcode-related tasks.
Step 9: Conduct a Trial Run
Test your system before full implementation:
- Start with a small section of your inventory.
- Identify and resolve any issues or bottlenecks.
- Gather feedback from staff and make necessary adjustments.
Step 10: Go Live and Monitor
Fully implement your barcode system:
- Roll out the system across your entire inventory.
- Continuously monitor performance and address any issues promptly.
- Regularly review and optimize your processes.
Best Practices for Barcode System Management
- Regular Audits: Conduct periodic inventory counts to ensure system accuracy.
- Backup Your Data: Regularly back up your inventory database to prevent data loss.
- Update Your System: Keep your software and hardware up-to-date for optimal performance.
- Maintain Equipment: Regularly clean and maintain your printers and scanners.
- Continuous Training: Provide ongoing training to staff as your system evolves barcode system implementation.
Common Challenges and Solutions
- Challenge: Poor barcode print quality Solution: Invest in a high-quality printer and regularly maintain it.
- Challenge: Resistance from staff Solution: Clearly communicate the benefits and provide comprehensive training.
- Challenge: Integration with existing systems Solution: Choose barcode software that offers robust integration capabilities or consider custom solutions.
- Challenge: Managing multiple locations Solution: Opt for cloud-based systems that allow real-time syncing across locations.
Future-Proofing Your Barcode System
As technology evolves, consider these future trends:
- Mobile Scanning: Leverage smartphones and tablets for barcode scanning.
- Cloud Integration: Move towards cloud-based inventory management for better accessibility and real-time updates.
- Advanced Analytics: Utilize big data analytics to gain deeper insights from your inventory data.
- IoT Integration: Explore Internet of Things (IoT) devices for automated inventory tracking.
Conclusion Barcode System Implementation
Implementing a barcode system is a significant step towards modernizing your small business operations. While the process may seem daunting, following this step-by-step guide will help ensure a smooth transition. Remember, the key to success lies in careful planning, choosing the right tools, and thorough staff training.
A well-implemented barcode system can transform your inventory management, leading to increased efficiency, reduced errors, and ultimately, improved profitability. As you grow more comfortable with the system, you’ll discover new ways to leverage this technology to streamline your operations and enhance your customer service.
How Linbis Can Help
Implementing a barcode system can be a complex process, especially for small businesses with limited resources. This is where Linbis comes in. As experts in logistics software development, Linbis offers both out-of-the-box solutions and custom development services tailored to the unique needs of small businesses.
Linbis can assist you at every stage of your barcode system implementation:
- Needs Assessment: Our team can help you evaluate your specific requirements and recommend the most suitable barcode solution.
- Software Selection and Development: Whether you need an off-the-shelf product or a custom-built solution, Linbis can provide or develop software that integrates seamlessly with your existing systems.
- Hardware Recommendations: We can advise on the best hardware options that fit your budget and operational needs.
- System Integration: Our experts ensure smooth integration of the barcode system with your existing inventory management, POS, or ERP systems.
- Staff Training: We provide comprehensive training to ensure your team is comfortable and proficient with the new system.
- Ongoing Support: Linbis offers continued support and updates to keep your barcode system running smoothly.
By partnering with Linbis, you gain access to our wealth of experience in implementing barcode systems across various industries. We understand the unique challenges faced by small businesses and can provide solutions that are not only powerful but also user-friendly and scalable.
Remember, while Linbis provides the technological foundation, the success of your barcode system ultimately depends on its strategic implementation within your unique business processes. Let Linbis be your guide in this important step towards improved efficiency and growth.