Automated Warehousing Systems: The Future of Supply Chain Management
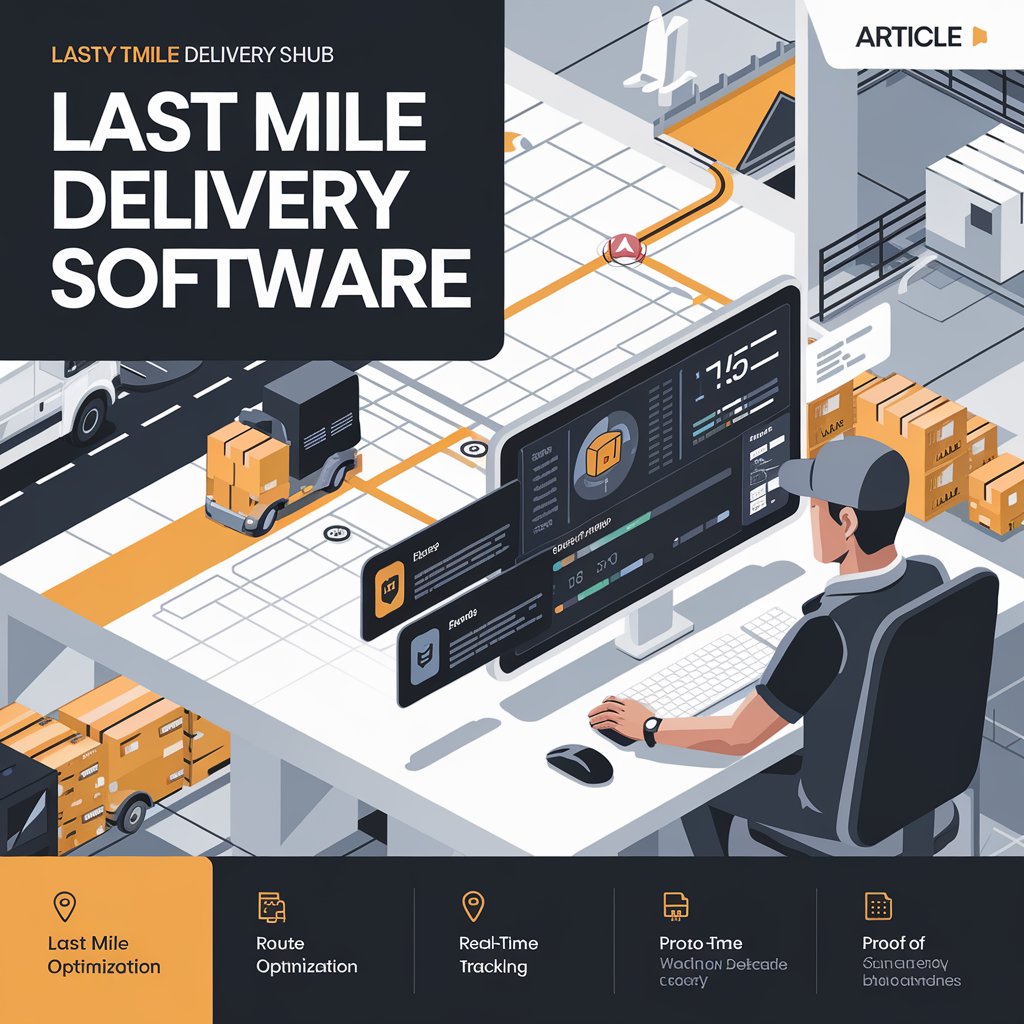
Understanding Automation in Warehousing: A Paradigm Shift
Warehouse automation refers to the use of technology and automated systems to improve the efficiency and accuracy of warehouse operations. These systems can range from simple barcode scanners to complex robotics and artificial intelligence. The goal is to minimize human intervention, reduce errors, and increase productivity.
Automated warehousing systems typically include:
- Automated Storage and Retrieval Systems (AS/RS)
- Automated Guided Vehicles (AGVs)
- Conveyor systems
- Robotic picking and packing systems
- Automated sorting systems
- Warehouse Management Systems (WMS)
By leveraging these technologies, businesses can significantly enhance their warehouse operations, leading to faster order fulfillment, reduced labor costs, and improved accuracy.
Linbis, a leader in logistics software, offers a comprehensive suite of tools that integrate seamlessly with automated warehousing systems. Their user-friendly platform ensures that businesses of all sizes can benefit from advanced automation capabilities without the need for extensive technical expertise.
The Benefits of Warehouse Automation
Implementing automated warehousing solutions can bring numerous advantages to your operations:
- Increased Efficiency: Automation can significantly speed up processes like picking, packing, and sorting, leading to faster order fulfillment.
- Improved Accuracy: Automated systems reduce human error, resulting in fewer mistakes in order picking and inventory management.
- Cost Reduction: While initial investment may be high, automation can lead to significant long-term cost savings through reduced labor costs and improved efficiency.
- Enhanced Safety: Automated systems can handle dangerous or repetitive tasks, reducing the risk of workplace injuries.
- Scalability: Automated systems can easily handle fluctuations in demand, making it easier to scale operations up or down as needed.
- Better Space Utilization: Many automated systems, like AS/RS, can maximize vertical space, leading to better warehouse space utilization.
- Improved Inventory Management: Automated systems provide real-time inventory tracking, reducing stockouts and overstock situations.
Linbis’s warehouse automation solutions are designed to maximize these benefits, offering a scalable platform that grows with your business. Their intuitive interface ensures that even non-technical users can quickly adapt to the system, maximizing productivity from day one.
Types of Warehouse Automation Technology
There are various types of warehouse automation technology, each suited to different aspects of warehouse operations:
- Goods-to-Person (GTP) Technology: This includes systems like AS/RS and carousels that bring items to workers for picking.
- Automated Guided Vehicles (AGVs): Self-driving vehicles that can transport goods around the warehouse.
- Robotic Picking Systems: Robots that can pick and pack items, often working alongside human workers.
- Conveyor Systems: Automated belts that move products through different areas of the warehouse.
- Sortation Systems: Automated systems that sort items based on predetermined criteria.
- Automated Packaging Systems: Machines that can measure, box, and label items automatically.
- Drones: Used for inventory counting and monitoring in large warehouses.
- Wearable Technology: Devices like smart glasses or wrist-mounted computers that provide workers with real-time information.
Linbis’s warehouse management system is designed to integrate seamlessly with all these types of automation technology, providing a unified platform for managing your entire warehouse operation.
Warehouse Automation Examples: Success Stories from the Field
To illustrate the real-world impact of automated warehousing systems, let’s look at a few success stories:
- E-commerce Giant Amazon: Amazon’s use of Kiva robots (now Amazon Robotics) has revolutionized their warehouse operations, significantly reducing order processing times.
- Grocery Chain Ocado: Ocado’s highly automated warehouses use a combination of AGVs, robotic picking systems, and AI to process thousands of orders daily.
- Fashion Retailer Uniqlo: Uniqlo’s automated warehouse in Tokyo uses an AS/RS system that has improved efficiency by 80% compared to their traditional warehouses.
- Pharmaceutical Distributor McKesson: McKesson’s use of robotic picking systems has led to a 99.9% accuracy rate in order fulfillment.
These examples demonstrate how automated warehousing systems can transform operations across various industries. Linbis has its own impressive portfolio of client success stories, showcasing how their integrated automation solutions have helped businesses overcome challenges and achieve significant improvements in their warehouse operations.
Implementing Automated Warehousing Solutions: Best Practices
Adopting automated warehousing systems requires careful planning and execution. Here are some best practices to ensure a successful implementation:
- Assess Your Needs: Conduct a thorough analysis of your current operations to identify areas where automation can bring the most benefit.
- Start Small: Begin with automating one process or area before expanding to full warehouse automation.
- Choose the Right Technology: Select automation solutions that align with your specific needs and can integrate with your existing systems.
- Train Your Team: Provide comprehensive training to all staff members who will be working with the new automated systems.
- Plan for Maintenance: Develop a maintenance schedule to ensure your automated systems continue to operate at peak efficiency.
- Monitor and Optimize: Regularly review system performance and make adjustments as needed to maximize efficiency.
- Consider Scalability: Choose solutions that can grow with your business to avoid the need for complete system overhauls in the future.
Linbis understands the importance of a smooth implementation process. Their team of experts works closely with clients to ensure a seamless transition, providing comprehensive training and support throughout the automation journey.
Overcoming Challenges in Warehouse Automation
While the benefits of automated warehousing systems are clear, implementation can come with its own set of challenges. Here are some common hurdles and strategies to overcome them:
- High Initial Costs: While automation can lead to long-term savings, the initial investment can be substantial. Consider starting with smaller automation projects and scaling up over time.
- Integration with Existing Systems: Ensuring new automated systems work seamlessly with existing warehouse management software can be challenging. Choose automation solutions with robust integration capabilities.
- Employee Resistance: Some employees may feel threatened by automation. Address these concerns through clear communication and training programs that emphasize how automation can enhance, rather than replace, human roles.
- Maintenance and Downtime: Automated systems require regular maintenance and can lead to significant disruptions if they break down. Develop robust maintenance schedules and have contingency plans in place.
- Flexibility: Some automated systems can be less flexible than human workers when dealing with unexpected situations. Maintain a balance between automation and human intervention.
Linbis’s experienced implementation team is well-versed in addressing these challenges. They work closely with clients to develop tailored solutions and provide ongoing support to ensure a smooth transition and maximum ROI.
The Future of Warehouse Automation: Emerging Trends
As technology continues to evolve, so does the landscape of warehouse automation. Here are some exciting trends shaping the future:
- Artificial Intelligence and Machine Learning: AI-powered systems can predict inventory needs, optimize picking routes, and enhance overall warehouse efficiency.
- Internet of Things (IoT): Connected devices and sensors provide real-time data on inventory levels, equipment status, and environmental conditions.
- Augmented Reality: AR technology can assist with picking accuracy and provide visual guides for warehouse layout optimization.
- Collaborative Robots (Cobots): These robots work alongside human workers, enhancing productivity while maintaining flexibility.
- Autonomous Mobile Robots (AMRs): More advanced than traditional AGVs, AMRs can navigate dynamically and make decisions based on their environment.
- Blockchain: Enhanced traceability and security for supply chain management.
- 5G Technology: Faster, more reliable connectivity will enable more sophisticated automation systems.
Linbis is at the forefront of these technological advancements, continuously updating its warehouse management platform to incorporate cutting-edge features. Their commitment to innovation ensures that clients always have access to the most advanced automation tools available.
Automated Warehouse Scenario: A Day in the Life of a Fully Automated Warehouse
To better understand the potential of automated warehousing systems, let’s walk through a typical day in a fully automated warehouse:
- Order Receipt: The warehouse management system receives orders automatically from various sales channels.
- Inventory Check: AI algorithms instantly check inventory levels and allocate stock to orders.
- Picking Process: AGVs or AS/RS systems retrieve the required items from storage locations.
- Sorting and Packing: Automated conveyor systems transport items to robotic packing stations where they are boxed and labeled.
- Quality Control: AI-powered computer vision systems perform a final check for accuracy.
- Shipping: The packed orders are automatically sorted based on shipping method and carrier.
- Replenishment: The system continuously monitors inventory levels and triggers automated replenishment processes as needed.
- Maintenance: Predictive maintenance algorithms schedule routine checks and repairs during off-peak hours.
This scenario demonstrates how automated warehousing systems can create a seamless, efficient operation with minimal human intervention. Linbis’s comprehensive warehouse management solution is designed to orchestrate all these processes, providing real-time visibility and control over the entire operation.
Small Warehouse Automation: Solutions for Growing Businesses
While large corporations often lead the way in warehouse automation, there are numerous solutions available for small and medium-sized businesses:
- Mobile Robots: Smaller, more affordable robots that can assist with picking and transport.
- Modular Conveyor Systems: Scalable conveyor solutions that can grow with your business.
- Cloud-Based WMS: Software solutions that provide advanced functionality without the need for extensive on-premise infrastructure.
- Pick-to-Light Systems: Affordable solutions that can significantly improve picking accuracy and speed.
- Automated Packaging Solutions: Machines that can automate the boxing and labeling process, suitable for smaller operations.
- Collaborative Robots: Flexible robotic solutions that can work alongside human workers in smaller spaces.
Linbis offers scalable automation solutions suitable for businesses of all sizes. Their cloud-based platform allows small warehouses to benefit from advanced automation features without the need for significant upfront investment in hardware or IT infrastructure.
Conclusion: Embracing the Future with Automated Warehousing Systems
As we’ve explored throughout this article, automated warehousing systems are revolutionizing the way businesses manage their supply chains. By offering unparalleled efficiency, accuracy, and scalability, these systems are empowering companies of all sizes to optimize their operations and stay competitive in an increasingly digital world.
From advanced robotics and AI-powered management systems to IoT sensors and predictive analytics, warehouse automation provides a comprehensive toolkit for modern supply chain management. As technology continues to evolve, we can expect even more exciting innovations in this space, further enhancing the capabilities of these powerful solutions.
For businesses looking to take their warehouse operations to the next level, adopting automated warehousing systems is no longer just an option – it’s a necessity. And when it comes to choosing the right provider, Linbis stands out as a leader in the field. With its user-friendly interface, robust feature set, and commitment to innovation, Linbis offers a comprehensive platform that can truly transform your warehouse operations.
Don’t let outdated systems hold your business back. Embrace the future of warehouse management with automated warehousing systems and discover the difference they can make for your organization. With Linbis, you’ll have a partner dedicated to your success, providing the tools and support you need to thrive in today’s fast-paced business environment.