Practical Tips for Freight Capacity Planning: Meeting Demand Efficiently
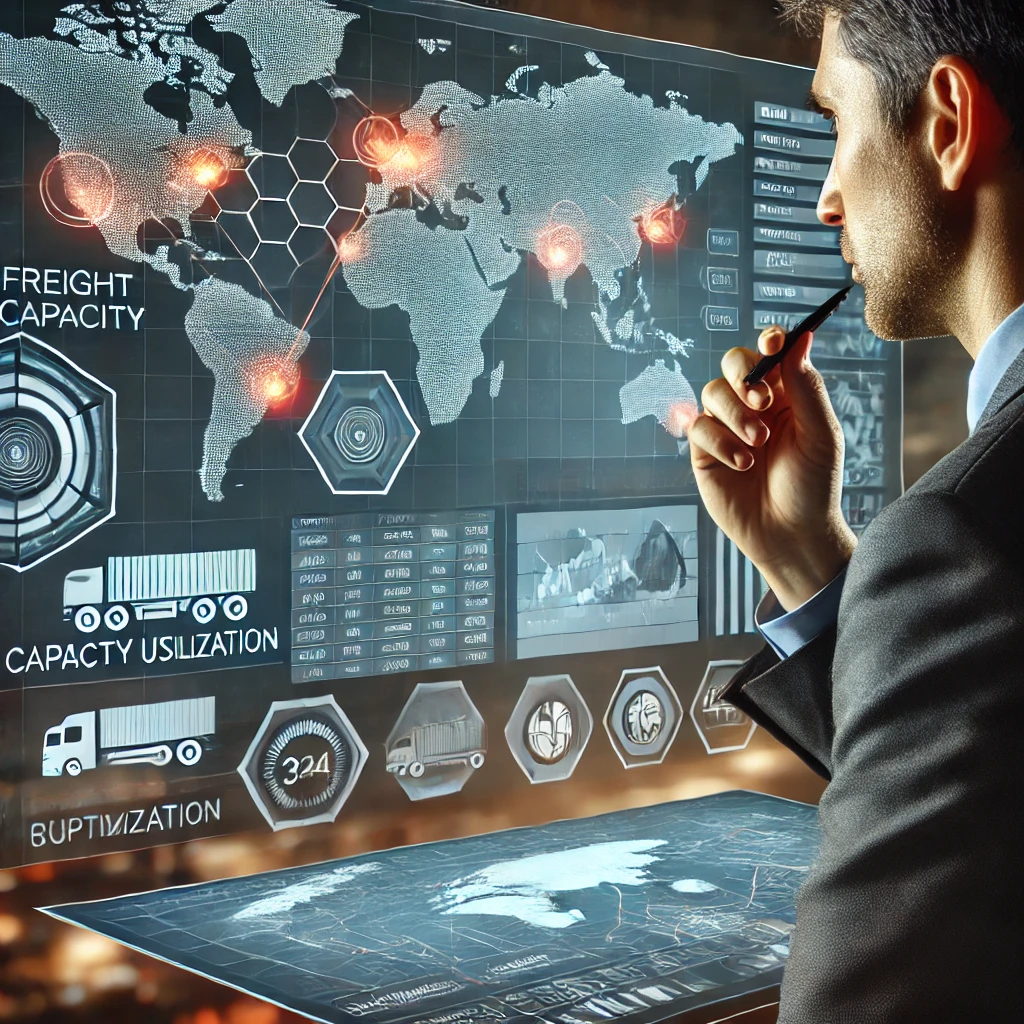
Why Freight Capacity Planning Is Important
Freight capacity planning involves forecasting and allocating resources (such as trucks, warehouses, and carriers) to meet the transportation needs of the business. The goal is to ensure that the right amount of freight capacity is available at the right time, without under or overutilizing resources. Effective capacity planning ensures that:
- Customer Demand Is Met: By aligning capacity with demand, businesses can ensure that customers receive their products on time, improving satisfaction and loyalty.
- Cost Efficiency: Proper capacity planning helps optimize resources, reducing waste and unnecessary costs, such as paying for empty miles or unused warehouse space.
- Minimized Disruptions: Effective planning helps prevent delays caused by a lack of capacity, reducing the risk of stockouts, order delays, or missed shipments.
- Better Resource Allocation: Efficient capacity planning allows businesses to allocate resources (personnel, trucks, storage space, etc.) in the most optimal manner, helping to avoid bottlenecks in the supply chain.
Key Tips for Effective Freight Capacity Planning
To help you achieve better freight capacity planning and meet demand effectively, here are some practical tips:
1. Analyze Historical Data and Forecast Demand
One of the first steps in freight capacity planning is understanding the patterns and trends of past demand. By analyzing historical data, you can identify peak seasons, off-peak periods, and other fluctuations that may impact your shipping needs.
- Review past shipments: Look at trends in order volumes, seasonal spikes, and market changes that affected transportation.
- Forecast future demand: Use historical data to predict future demand more accurately. Incorporate external factors such as industry growth, consumer trends, and potential disruptions (e.g., economic downturns or natural disasters).
Tools for Demand Forecasting:
- ERP Systems: Many Enterprise Resource Planning systems include features for demand forecasting.
- Data Analytics Platforms: Tools like Power BI, Tableau, or Excel can help you analyze past data to spot trends and create forecasts.
2. Build Strong Relationships with Freight Providers
Developing good relationships with freight providers and carriers can help ensure that you have reliable access to the capacity you need when demand spikes.
- Collaborate with key partners: Work with your carriers to understand their capacity, lead times, and pricing. This helps ensure that your transportation needs are met when required.
- Diversify your carriers: Don’t rely on a single carrier. Establish relationships with multiple providers to give you flexibility when unexpected spikes in demand arise.
- Negotiate contracts: With long-term partners, negotiate contracts that guarantee certain capacity levels, allowing you to plan more effectively.
3. Use Technology to Optimize Planning
Today’s freight planning technologies can offer a wealth of features to improve capacity planning efficiency. By automating certain aspects of the planning process, you can reduce human error and increase your ability to manage capacity.
- Transportation Management Systems (TMS): A TMS can help you optimize routes, track carrier availability, and forecast demand, making it easier to plan your freight capacity.
- Artificial Intelligence and Machine Learning: AI-driven systems can analyze vast amounts of data to predict demand fluctuations and suggest optimal shipping routes, helping you avoid over-committing resources.
- Real-Time Tracking: Real-time tracking allows you to adjust capacity dynamically, allocating resources as demand increases or decreases during transportation.
4. Prioritize Flexible Capacity Options
Freight capacity needs can change rapidly due to fluctuating demand. Therefore, you must have access to flexible capacity options that allow you to scale up or down quickly.
- On-Demand Freight Solutions: Consider utilizing on-demand freight options that can quickly adjust to sudden increases in demand. Services like spot market carriers and crowdsourced logistics providers can provide additional capacity during peak periods.
- Leverage Multi-modal Transport: When necessary, consider switching between different modes of transport (e.g., from truck to rail or air to sea) to optimize capacity and reduce costs. Multi-modal planning can provide flexibility when one mode reaches its capacity limits.
5. Monitor and Adjust Plans in Real-Time
Freight capacity planning isn’t a set-it-and-forget-it task. In order to meet fluctuating demand, you need to continually monitor your shipments and make adjustments in real time.
- Track progress regularly: Use tracking tools to monitor shipments, ensuring that you stay informed about delivery statuses and potential delays.
- Be proactive with adjustments: If demand increases unexpectedly, quickly adjust by activating backup carriers or utilizing additional transport modes.
- Create contingency plans: Have backup options and contingency plans in place for unexpected surges in demand or supply chain disruptions.
Real-Time Tracking Tools:
- Project44 and FourKites are excellent platforms for real-time shipment visibility and capacity management.
6. Optimize Warehouse and Storage Capacity
In many cases, freight capacity planning isn’t limited to transportation alone—it also includes warehouse and storage planning. Poor warehouse capacity can create bottlenecks in the supply chain and prevent the timely flow of goods.
- Increase warehouse efficiency: Ensure that your warehouse is optimized to handle fluctuations in stock and prevent bottlenecks. This might include using automated systems, improving layout designs, and implementing just-in-time inventory strategies.
- Coordinate with transportation teams: Warehouse and transportation teams need to collaborate to ensure that goods are loaded onto trucks in a timely manner to avoid delays.
7. Consider the Impact of Seasonal Demand
Certain industries experience significant seasonal variations in demand. For example, the retail sector sees peak demand during the holiday season, while agricultural products may have specific harvest cycles. Effective freight capacity planning must take these seasonal shifts into account.
- Plan for peaks: During peak seasons, it’s critical to ensure you have sufficient capacity by securing extra carriers or increasing warehouse space ahead of time.
- Account for off-peak periods: Similarly, during slower periods, you may want to scale back your capacity to avoid overutilizing resources and incurring unnecessary costs.
8. Maintain a Balance Between Capacity and Costs
While it’s important to meet demand, it’s also crucial to ensure that you don’t overcommit resources that will not be fully utilized. The goal is to achieve a balance between meeting customer demand and managing costs effectively.
- Evaluate capacity costs: Regularly assess the cost implications of maintaining high or low levels of capacity. For example, investing in extra warehouse space or leasing additional vehicles may make sense during peak periods but may not be sustainable during off-seasons.
- Analyze cost-to-capacity ratios: Optimize the cost-to-capacity ratio by focusing on demand forecasting and cost-effective resources.
Conclusion
Effective freight capacity planning is essential for ensuring that you meet customer demand without overburdening your resources or incurring unnecessary costs. By following these practical tips—analyzing historical data, building relationships with carriers, utilizing technology, and remaining flexible—you can optimize your freight capacity management and improve the overall efficiency of your supply chain. As the market evolves and demand shifts, staying ahead of capacity challenges will be crucial to your business’s ability to thrive in a competitive logistics landscape.