Warehouse Optimization: Strategies for Enhancing Efficiency and Productivity
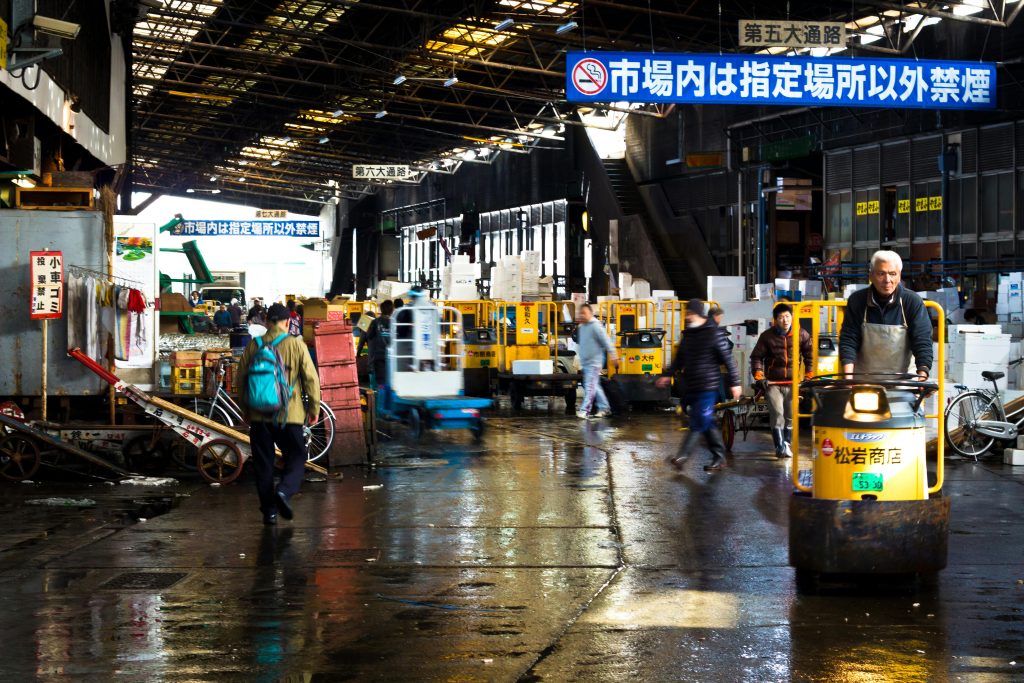
Understanding Warehouse Optimization
Warehouse optimization refers to the process of improving the efficiency and effectiveness of warehouse operations. It encompasses a wide range of activities, from layout design and inventory management to process streamlining and technology integration. The ultimate goal is to maximize productivity, reduce costs, and improve customer satisfaction.
Key components of warehouse optimization include:
- Space utilization
- Inventory management
- Order fulfillment processes
- Labor efficiency
- Technology integration
The benefits of optimizing warehouse operations are numerous:
- Reduced operational costs
- Improved order accuracy and speed
- Enhanced inventory control
- Better utilization of warehouse space
- Increased labor productivity
- Improved customer satisfaction
Warehouse Optimization Techniques
1. Layout and Space Utilization
Effective warehouse layout is fundamental to optimization. A well-designed layout can significantly reduce travel time, improve picking efficiency, and maximize storage capacity. Consider the following strategies:
- Implement a logical flow of goods from receiving to shipping
- Use vertical space effectively with appropriate racking systems
- Design aisles to accommodate equipment and optimize picking routes
- Create designated areas for different activities (receiving, packing, shipping)
2. Inventory Management
Efficient inventory management is crucial for warehouse optimization. Implement the following techniques:
- Use ABC analysis to prioritize inventory based on value and turnover
- Implement cycle counting for accurate inventory tracking
- Optimize reorder points and safety stock levels
- Use demand forecasting to anticipate inventory needs
3. Technology Integration
Modern warehouses rely heavily on technology for optimization. Key technologies include:
- Warehouse Management Systems (WMS) for overall coordination
- Barcode scanners and RFID for accurate tracking
- Automated Storage and Retrieval Systems (AS/RS)
- Internet of Things (IoT) sensors for real-time monitoring
4. Process Streamlining
Continuously evaluate and improve warehouse processes:
- Implement lean principles to eliminate waste
- Use cross-docking to reduce handling and storage time
- Optimize picking strategies (wave picking, batch picking, etc.)
- Standardize processes for consistency and efficiency
5. Staff Training and Development
Well-trained staff are essential for warehouse optimization:
- Provide comprehensive training on equipment and procedures
- Cross-train employees for flexibility
- Implement performance metrics and incentives
- Encourage employee feedback for continuous improvement
Implementing a Warehouse Optimization Project
Implementing a warehouse optimization project requires careful planning and execution. Follow these steps:
- Assessment: Conduct a thorough analysis of current operations, identifying bottlenecks and inefficiencies.
- Goal Setting: Define clear, measurable objectives for the optimization project.
- Planning: Develop a detailed plan, including timelines, resource allocation, and budget.
- Implementation: Execute the plan in phases, starting with quick wins to build momentum.
- Monitoring and Adjustment: Continuously monitor progress and make necessary adjustments.
- Review and Iterate: Regularly review the results and plan for ongoing improvements.
Common challenges in warehouse optimization projects include:
- Resistance to change from staff
- Integration issues with existing systems
- Budget constraints
- Balancing short-term disruptions with long-term benefits
To overcome these challenges, focus on clear communication, involve stakeholders early in the process, and emphasize the long-term benefits of optimization.
Measuring the Success of Optimization Efforts
To gauge the effectiveness of your warehouse optimization efforts, track key performance indicators (KPIs) such as:
- Order accuracy rate
- Order fulfillment time
- Inventory turnover ratio
- Warehouse capacity utilization
- Labor productivity
- Cost per order
Utilize analytics tools within your Warehouse Management System to track these metrics and generate regular reports. This data-driven approach allows for continuous improvement and helps identify areas that may need further optimization.
How Linbis Supports Warehouse Optimization
Linbis offers a comprehensive suite of tools designed to support warehouse optimization efforts. Our state-of-the-art Warehouse Management System provides:
- Real-time inventory tracking and management
- Advanced picking and packing algorithms
- Labor management and performance tracking
- Customizable reporting and analytics
- Integration with various warehouse technologies
Linbis has helped numerous companies achieve significant improvements in their warehouse operations. For example, a mid-sized e-commerce company implemented Linbis’s WMS and saw a 30% increase in order fulfillment speed and a 25% reduction in picking errors within the first six months.
Tips for Continuous Warehouse Optimization
Warehouse optimization is not a one-time event but an ongoing process. Here are some tips for maintaining a culture of continuous improvement:
- Regular Audits: Conduct periodic audits of warehouse operations to identify areas for improvement.
- Stay Informed: Keep up with industry trends and new technologies that could benefit your operations.
- Employee Involvement: Encourage employees to suggest improvements and recognize their contributions.
- Data Analysis: Regularly analyze performance data to identify trends and opportunities for optimization.
- Flexibility: Be prepared to adapt your optimization strategies as business needs change.
- Technology Updates: Regularly update and upgrade your warehouse management software to take advantage of new features and improvements.
Conclusion
Warehouse optimization is a critical factor in maintaining a competitive edge in today’s fast-paced business environment. By implementing the strategies outlined in this article and leveraging advanced tools like Linbis’s Warehouse Management System, companies can significantly enhance their warehouse efficiency and productivity.
Remember, optimization is an ongoing journey rather than a destination. Continuously assess your operations, stay open to new ideas and technologies, and be willing to adapt your strategies as needed. With a commitment to continuous improvement and the right tools at your disposal, your warehouse can become a powerful asset driving your business’s success.
Are you ready to take your warehouse operations to the next level? Explore how Linbis can support your optimization journey and help you achieve new heights of efficiency and productivity.